Keywords: natural dyes, walnut, wool, cotton, mordant, aluminum acetate, potassium aluminum sulfate, textile
Abstract
The purpose of this research was to compare mordanted and nonmordanted cotton and wool fabrics, dyed with black walnut (Juglans nigra) leaves, hulls, and bark for colorfastness properties. Half of the cotton fabrics were mordanted with aluminum acetate and half of the wool fabrics were mordanted with potassium aluminum sulfate. Colorfastness to laundry and light for both cotton and wool were improved with the use of an aluminum mordant. However, the use of a mordant changed the color from a cool (blue) and dull brown to a warmer (yellow) and brighter brown. Overall, walnut bark dyed wool had the highest ratings for both fastness to laundry and light.
Introduction and Literature Review
Research into natural dyes is important due to the renewed interest shown in environmentally responsible practices: buying local and artisan dying. Natural dyes have many advantages over synthetic dyes, such as their ecologically sustainable properties, and (depending on the mordant) they are relatively free of poisonous chemicals (Flint, 2008). It is important to note that drawbacks such as inherently poor colorfastness and the need for a greater amount of dye matter has slowed down use of natural dyes and makes them a poor sole substitute for synthetic dyes (Flint, 2008). However, synthetic dyes are known to have had adverse affects on the health of workers and have poisoned previously drinkable water (Flint, 2008). Thus, the environmental and safety concerns make research of environmentally responsible natural dye practices an important goal.
Walnuts hulls and bark have been used as a brown dye throughout the history of dyeing. The black walnut tree (Juglans nigra L) is native to North America and grows up to 50 m high, with fruit that is globose and leaves that are oblong and serrated (Cardon, 2007). The Meskwaki tribe of the Great Lakes and later Iowa created black dye powder from the wood and bark (Cardon, 2007). European colonists used black walnut bark for dyeing yarn and home-made textiles or homespuns (Mell, 1930). Many southern states used the root bark of the walnut tree to dye Confederate soldier uniforms and the use of this natural dyestuff remained in high demand through the end of the Civil War (Mell, 1930). Kansas pioneers recall using walnut bark to produce browns and grays on unbleached muslim and home spun wool yarn (Richards & Tyrl, 2005).
Walnut dye is considered a substantive or direct dye, which produces durable colors without the addition of a mordant to assist with the bond between dye and fiber (Richards & Tryl, 2005). Mordants are metallic salts or naturally occurring chemicals that cause the color from the chromospheres to adhere to the yarns being dyed (Richards & Tyrl, 2009). The most common metallic salts used are aluminum, tin, iron, and copper. The high content (approx. 4%) of tannins in walnut hulls, bark, and leaves serve as a natural mordant (Cardon, 2007).
Even though fibers dyed with walnut do not require a mordant, the use of an aluminum mordant has been noted to make colors more fast and shift the color slightly toward yellow or red (Mell, 1930; Van Stralen, 1993). Despite the abundance of fallen walnut fruit or hulls in late summer and early fall and the inclusion of black walnut dyeing procedures in books on natural dyeing, limited research has been published on the fastness properties of walnut dye. Sharma and Grover (2011) examined cotton yarns dyed with walnut (Julgans regia Linn) bark and mordanted with alum, copper sulphate, ferrous sulphate, and chrome for colorfastness of washing, light, crocking, and perspiration. The results for all tests and all mordants were satisfactory with gray scale ratings ranging from 3-4 (noticeable/slight) to 5 (no change) and the lightfastness ratings 6 to 8 (very good to excellent). Another reference to cotton having an affinity to walnut hulls was noted by Mell (1930) as "very durable" (p. 460) when referencing the 1841 dye book by Berthlolett. This statement and the findings by Sharma and Grover (2011) implore the natural dye researcher to investigate as cotton is typically not known for its affinity to most natural dyes.
Purpose and Hypotheses
It has been stated that an aluminum mordant increases the fastness properties of walnut dye; however, no research was found that compared mordanted and nonmordanted walnut dyed fibers. Therefore, the purpose of this research was to compare mordanted and nonmordanted cotton and wool fabrics, dyed with black walnut (Juglans nigra L) leaves, hulls, and bark for colorfastness properties. The mordants used were aluminum acetate for the cotton fabric and potassium aluminum sulfate for the wool fabric as recommended by Wipplinger (2005) and Dean (2009). These mordants were selected due to their nontoxic nature and availability to natural dye artisans. This study addressed the following hypotheses:
- Fabrics premordanted with an aluminum mordant and dyed with walnut dyestuffs will have higher gray scale ratings than fabrics without a premordant on tests of colorfastness to
- Laundry
- Light
- Fabrics premordanted with an aluminum mordant and dyed with walnut dyestuffs will have a color change towards yellow.
Methods
Materials
Experimental fabrics. The fabrics used in the study were a 100 percent wool and a 100 percent cotton, both from Testfabrics, Inc. The wool was style number 541, a worsted gabardine naturally scoured fabric. The cotton was style number 400M, a bleached desized mercerized cotton print cloth. A wool fabric was selected due to its natural affinity and history with natural dyes. The gabardine was selected for its comparatively lighter weight. A cotton fabric was selected as cotton was found by Sharma and Grover (2011) to have good to excellent fastness properties. The mercerized cotton was selected in particular as mercerization can increase absorbency and dyeability (Kadolph & Langford, 2002).
Scouring Agents. All samples were pre-washed, called scouring, to remove any impurities with a professional textile detergent (liquid scour) and sodium carbonate (soda ash) from Hillcreek Fiber Studios. Both the liquid scour and soda ash are available to artisans and home dyers and were used because the results of this study may benefit natural dye artisans.
Mordants. The cotton print cloth was premordanted with aluminum acetate, purchased from Hillcreek Fiber Studio. The wool gabardine was premordanted with potassium aluminum sulfate and cream of tartar, also purchased from Hillcreek Fiber Studio. Only half of the cotton and wool samples were premordanted in order to compare the differences between mordanted and nonmordanted samples.
Natural dyestuffs. The natural dyestuffs used were black walnut (Juglans nigra L) leaves, bark, and hulls. Fresh plant matter was collected locally (from a central plains state) during the early summer and into the fall. The dye material was air dried, then ground with a food processer and pestle and mortar to refine the product.
Scouring, Mordanting and Dyeing Procedures
Scouring. Test samples were cut to weigh 7±0.02 g and edges finished with an overlock stitch in 100% polyester thread. All samples were scoured in a bath of 2 percent sodium carbonate to weight of fiber (WOF), 5.5 percent liquid scour to WOF and a ratio of 80:1 (liquor-to-dry goods) or 560 ml of reverse osmosis (RO) water. Approximately 30 minutes before scouring the 7 g samples were completely covered in RO water to ensure a more even uptake. The wetted samples, dissolved sodium carbonate, liquid scour, and RO water (heated to approximately 80 °C) were then added to individual Atlas Launder-Ometer stainless steel canisters and shaken 6-7 times by hand to begin agitation. The Launder-Ometer rotates the canisters in a thermostatically controlled water bath. The temperature raised from 25 °C to 80 °C over 90 minutes and then cooled down to 25 °C over 20 minutes. The samples were then removed from the canisters, rinsed under RO water for 30 seconds, and laid flat to air dry.
Premordanting. Half of the cotton and wool scoured samples were then premordanted. The wool samples were premordanted using a treatment of 12 percent potassium aluminum sulfate to WOF, 6 percent cream of tartar to WOF and an 80:1 liquor-to-dry goods ratio of RO water. The cotton samples were premordanted using a treatment of 5 percent aluminum acetate and 80:1 liquor-to-dry goods ratio of RO water. All samples were wetted out for 30 minutes in RO water before premordanting began. The respective dissolved mordants, RO water, and samples were added to individual Atlas Launder-Ometer stainless steel canisters and shaken 6-7 times by hand to begin agitation. The canisters were run in an Atlas Launder-Ometer for 90 minutes with the temperature raised from 25 °C to 80 °C and then cooled down to 25 °C over 20 minutes. The samples were then removed from the canisters, rinsed under RO water for 30 seconds, and laid flat to air dry.
Dye extraction. The dye was extracted by placing 210 grams of the dyestuff in a large aluminum stock pot and covering in 1200 ml of hot RO water (approximately 80 °C). The dye bath was kept at 80 °C for two hours with agitation occurring every five to ten minutes and then cooled and left to soak for 48 hours. The plant material was sifted out of the dye bath and additional water was added to each dye bath due to water lost during evaporation. There were three dye baths for each dyestuff (i.e., leaves, hulls, bark).
Dyeing samples. Three dye baths of each individual dyestuff was split up into four aliquots, and additional water was added for the dyeing stage. Samples were randomly assigned to each dye bath. To dye the samples, 560 ml of dye solution was poured into individual Launder-Ometer canisters, follow by the wetted out sample. Over 90 minutes the temperature was raised from 25 °C to 80 °C and then cooled down to 25 °C over 20 minutes. The samples were removed from the canisters, rinsed in RO water, laid flat to air dry, and pressed with a hot iron for ten seconds.
Tests for Colorfastness to Light and Laundering
Test specimens were cut from the dyed samples according to AATCC Test Methods 16-2004 and 61-2007 (AATCC, 2009) and evaluated for lightfastness and washfastness. Lightfastness testing was conducted by Atlas Weathering Services Group, IL, using an Atlas Xenon Weather-Ometer and was exposed to continuous light for 20 AATCC fading units (AFU). Procedures were conducted following the AATCC Test Method 16-2004, Colorfastness to Light, Option 3 (AATCC, 2009).
Colorfastness to laundering testing was conducted in-house in accordance with AATCC Test Method 61-2007, Colorfastness to Laundering, Home and Commercial: Accelerated, Test No. 2A. This is to evaluate textiles that are expected to withstand repeated low temperature machine launderings and simulates five machine launderings at warm temperature settings in the range of 38 ± 3°C (AATCC, 2009). Specimens were placed in stainless steel containers with 150 ml of RO water, .15 percent (weight of total volume) AATCC testing detergent and 50 steel balls. The containers were then placed in an Atlas Launder-Ometer, which rotated the canisters in a thermostatically controlled water bath. After laundering, specimens were rinsed three consecutive times in beakers of RO water for one minute each.
Color Evaluation Procedures
The specimens exposed to 20 AFU's of Xenon light were evaluated visually by Professional Testing Labs and the laundering tests were evaluated in-house by three evaluators who had normal color vision. Color change in washfastness specimens were assessed following AATCC Evaluation Procedure 1, Gray Scale for Color Change (AATCC, 2009). Color differences between the nonmordanted and mordanted specimens were evaluated according to AATCC Procedure 9-2007, Visual Assessment of Color Difference of Textiles (AATCC, 2009).
Results and Discussion
The purpose of this research was to compare premordanted and nonmordanted cotton and wool fabrics dyed with black walnut leaf, hull, and bark. Nonmordanted and mordanted samples were compared for performance in colorfastness to laundry and light and for color change.
Colorfastness to Laundering Results
Cotton. Overall, the premordanted cotton specimens performed better than the nonmordanted specimens when tested for washfastness (Table 1). The nonmordanted cotton specimens dyed with walnut leaves had an average gray scale rating of 4 to 5, or slight to no change, while the mordanted specimens had an average rating of 5 or no change when compared to the standard. This high rating of colorfastness could be due to the small amount of dye color retrieved from the leaves, thus leaving little dye to lose. The hull dyed premordanted cotton performed somewhat better than the nonmordanted cotton, with noticeable compared to considerable color change. Mordanted cotton specimens dyed with walnut bark performed better than the nonmordanted specimens with slight change (4) and considerable/noticeable (2-3) change of color respectively. This rating of 4 or slight change for cotton dyed with walnut bark approaches the Sharma and Grover (2011) rating of 5 or no change for walnut bark on alum premordanted cotton.
Table 1. Colorfastness to Laundering of Walnut Leaf, Hull, and Bark on Cotton and Wool with No Mordant and Aluminum Mordant.
|
Cotton
|
Wool
|
No Mordant
|
Aluminum
Acetate
|
No Mordant
|
Potassium
Aluminum
Sulfate
|
Leaf
|
4-5
|
5
|
4
|
4
|
Hull
|
2
|
3
|
4-5
|
4-5
|
Bark
|
2-3
|
4
|
5
|
5
|
Note: Color change ratings: 5 = none, 4 = slight, 3 = noticeable, 2 = considerable, 1 = severe.
Wool. The wool premordanted and mordanted specimens performed equally when tested for washfastness, with the bark specimens continuing to be the most colorfast. See Table 1. Both nonmordanted and mordanted specimens dyed with walnut leaves had an average gray scale rating of 4 or slight color change when compared to the standard. Nonmordanted and mordanted specimens dyed with walnut hulls had an average gray scale rating of 4 to 5, or slight to equal. While nonmordanted and mordanted specimens dyed with bark had an average rating of 5, or none, meaning that there was no change between the washfastness specimens and the standard. Overall, the premordanted cotton and both the non- and premordanted wool had washfastness performance acceptable for apparel and home furnishings (ASTM, 2002). With the exception of the leaf, wool had better washfastness than the cotton.
Colorfastness to Light Results
Cotton. Cotton specimens in general performed poorly when exposed to 20 AFU's and the aid of a mordant had little to no affect (Table 2). Nonmordanted and mordanted cotton specimens that were dyed with walnut leaves both had a 1 to 2 rating, or severe to considerable difference, when compared to the standard. This could be due to less tannin found in walnut leaves, less dye extracted from the leaves, and the cottons inability to hold the natural dye. Nonmordanted cotton fabric dyed with walnut hulls had a 2 rating, or considerable change, with the mordanted cotton rating 1 to 2 or severe to considerable change. Nonmordanted cotton fabric dyed with walnut bark had a rating of 2, or considerable difference while the mordanted cotton fabric dyed with walnut bark performed slightly better with a 2 to 3 rating, or considerable to noticeable difference, when compared to the standard. Therefore, none of the cotton fabrics dyed with walnut performed at a level high enough (i.e., a rating of 3 or higher) for use in apparel and home furnishings as determined by the Annual Book of ASTM Standards [ASTM], (2002). In addition, the lightfastness ratings did not meet the expectations set by Sharma and Grover (2011) who reported good to excellent lightfastness of walnut bark dyed cotton.
Table 2. Lightfastness (20 AFU's) of Walnut Leaf, Hull, and Bark on Cotton and Wool with No Mordant and Aluminum Mordant.
|
Cotton
|
Wool
|
No Mordant
|
Aluminum
Acetate
|
No Mordant
|
Potassium
Aluminum
Sulfate
|
Leaf
|
1-2
|
1-2
|
2-3
|
4-5
|
Hull
|
2
|
1-2
|
2
|
3-4
|
Bark
|
2
|
2-3
|
3-4
|
4-5
|
Note: Color change ratings: 5 = none, 4 = slight, 3 = noticeable, 2 = considerable, 1 = severe.
Wool. Overall, the premordanted wool specimens performed better than the nonmordanted specimens and better than cotton when exposed to 20 AFU's (Table 2). Nonmordanted wool specimens dyed with walnut leaves had an average gray scale rating of 2 to 3, or considerable to noticeable difference in color change, while mordanted specimens dyed with leaves performed better with a 4 to 5, or slight to no change when compared to the standard. Nonmordanted specimens dyed with walnut hulls had average rating of 2 or considerable difference in color change, while mordanted specimens dyed with hulls had an average rating of 3-4 or noticeable difference to slight in color change. Wool dyed with bark performed the best overall with a gray scale rating of 3 to 4, or noticeable to slight change, for the nonmordanted specimens and a 4 to 5, or slight to equal change, for the mordanted specimens. The premordanted wool dyed with walnut bark, hulls and leaves performed better than the nonmordanted samples with bark and leaves having little to no fading. These findings support the wool's affinity with natural dyes. The lightfastness results for wool dyed with walnut dyestuffs indicate that a mordant improves resistance to fading.
Visual Assessment of Color Change Between Mordanted and Nonmordanted Fabrics
The nonmordanted and mordanted specimens were compared for color differences in chroma, hue, and lightness. Any differences were given a rating as follows: 0 - off shade, 1 - much, 2 - considerable, 3 - noticeable, 4 - light, and 5 - no change. Overall the cotton fabric took to all walnut dye poorly, with or without a mordant, yielding a light tan hue. See Table 3. Only bark dyed cotton had a slight difference in lightness, with the premordanted specimens slightly darker. Leaf and hull had no color changes between cotton specimens with or without a mordant. These findings support the statement that walnut dyestuffs do not require a mordant. However, the resulting color is so light that the range of color differences possible is minimal.
Table 3. Visual Examples Comparing Nonmordanted and Premordanted Cotton and Wool Specimens Dyed with Walnut Leaf, Hull and Bark.
|
Cotton
|
Wool
|
No mordant
|
Aluminum
Acetate
|
No mordant
|
Potassium
Aluminum
Sulfate
|
Leaf
|
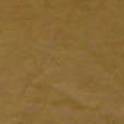
|
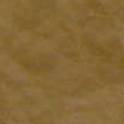
|
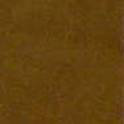
|
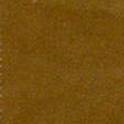
|
Hull
|
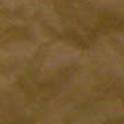
|
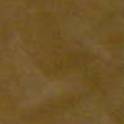
|
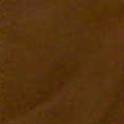
|
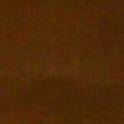
|
Bark
|
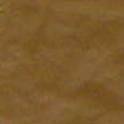
|
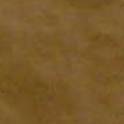
|
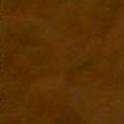
|
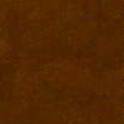
|
The wool samples took the dye especially well and all premordanted specimens were slightly to noticeably brighter, yellower, and darker. The wool dyed with walnut leaves appeared a golden brown, which was noticeably brighter and yellower with the premordant. Wool dyed with hulls also had noticeable differences between nonmordanted and mordanted samples. Nonmordanted samples were noticeably bluer and duller, while the mordanted wool samples were noticeably brighter and yellower. Wool dyed with bark had a slight color change between nonmardanted and mordanted specimens, with the mordanted specimens being slightly brighter and yellower when compared to the nonmordanted samples. These results support the comments by Van Stralen (1993) and Mell (1930) that an alum mordant will shift walnut hull dyed fibers slightly to yellow.
Conclusions and Recommendations for Further Study
The purpose of this research was to compare aluminum mordanted and nonmordanted cotton and wool fabrics dyed with black walnut leaves, hulls, and bark for colorfastness properties. The research hypotheses proposed in this study were answered by analyzing the colorfastness results.
-
Fabrics premordanted with an aluminum mordant and dyed with walnut dyestuffs will have higher gray scale ratings than fabrics without a premordant on tests of colorfastness to
- Laundry. Cotton results supported the hypothesis as the premordanted samples had a higher gray scale rating by one-half to a full step. Cotton premordanted and dyed with walnut bark showed the most improvement, moving form considerable/noticeable change to slight change. Wool results did not support the hypothesis as there was no color differences between mordant and non-mordanted specimens.
- Light. Cotton gray scale results did not support the hypotheses as there was considerable fading with our without a mordant. Colorfastness results for wool supported the hypotheses as the aluminum potassium sulfate mordant improved resistance to fading. All premordanted wool specimens outperformed the nonmordanted specimens by at least one full step on the gray scale for color change. Premordanted wool dyed with leaves or bark performed the best with slight to no change in color.
- Fabrics premordanted with an aluminum mordant and dyed with walnut dyestuffs will have a color change towards yellow. Little difference in color change was found between nonmordanted cotton specimens and specimens premordanted with aluminum acetate, thus cotton did not support the hypothesis. More of a difference could be determined between nonmordanted wool samples and wool that was premordanted with potassium aluminum sulfate. Premordanted wool specimens were consistently warmer, yellower, and brighter compared to nonmordanted test specimens.
Future studies into wool dyed with walnut dyestuffs could be expanded with tests for perspiration and crocking, along with varying the mordant amount and type. Studies could also test different fibers (e.g., silk) and fabric structures (e.g., knits).
In summary, colorfastness to laundry for cotton and colorfastness to light for wool were improved with the use of an aluminum mordant. The use of a mordant changed the color of wool from a cool (blue) and dull brown to a warmer (yellow) and brighter brown. Overall, walnut bark dyed wool had the highest ratings for both washfastness and lightfastness. Walnut dyestuffs are worthy of attention from artisans and researchers as they have an affinity for wool, are nontoxic, and colorfast, making future research important for environmentally responsible practices.
References
American Association of Textile Chemists and Colorists. (2009). 2009 Technical Manual of the American Association of Textile Chemists and Colorists (Vol. 84). Research Triangle Park, N. C.
Annual Book of ASTM Standards (2002), Section seven: Textiles (vol. 7-2), Bailey, S. J.,
Cardon, D. (2007). Natural dyes: Sources, tradition, technology and science. London, England: Archetype Publications Ltd.
Carol Leigh's hillcreek fiber studio. Retrieved, 2011, from http://www.hillcreekfiberstudio.com
Dean, J. (2009). Colours from nature: A dyer's handbook. Kent, England: Search Press Limited.
Flint, I. (2008). Eco colour: Botanical dyes for beautiful textiles. Millers Point, Australia: Murdoch Books.
Kadolph, S. J., & Langford, A. L. (2002). Textiles (9th ed.). Upper Saddle River, NJ: Pearson Education.
Mell, C. D. (1930). Walnut as a source of brown dyes. Textile Colorist, (52), 460.
Richards, L., & Tyrl, R. (2005). Dyes from American native plants: A practical guide. Portland, Or: Timber Press.
Sharma, A., & Grover, E. (2011). Colour fastness of walnut dye on cotton. Indian Journal of Natural Products and Resources, 2(2), 164-169.
Van Stralen, T. (1993). Indigo, madder and marigold: A portfolio of colors from natural dyes. Loveland, CO: Interweave Press.
Wipplinger, M. (2005). Natural dye instruction booklet. Seattle, WA: Earthues.